Testing for foam
Foams are used in a variety of applications in ranging from the absorption of energy, the protection of components and in comfort situations. For these purposes, a variety of foams have been designed with widely varying properties tailored specifically to each end use. In fact, this variability is one of the key factors contributing to the complexity of foam modelling. Foams are created with two important variables: the matrix material and the morphology of the gaseous phase. There are two generic morphologies; open cell and closed cell. The pore size plays a role in the behaviour, controlling the rate at which the gas exits the foam when it is compressed. The matrix can be made from a variety of material, rigid or flexible. Rigid materials typically result in crushable foams. Crushable foams undergo deformation by ductile plasticity or brittle means. In ductile behaviour, the foam walls undergo plastic deformation with little or no recovery. The cell walls in brittle foams fail, on the other hand, and there is no recovery. Rigid polyurethane and metal foams fail in this manner. Flexible materials are also used in foams. Common materials are plastics and rubber. Elastomeric foams are highly flexible, with high levels of recovery. The recovery may be instantaneous or over a period of time. Flexible polyurethane foams are typical of this class. Dense foams based on rubber are also made. Elastomeric foams tend to be open cell in nature.
TestPaks typically ordered for foam
Tests typically ordered for foam
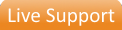